Highest levels of product purity and quality are of primary importance, particularly in such industries as the beverage, dairy, food and pharmaceutical industry. Independent Integrity Inspection Limited supports you in implementing your quality management routine by providing comprehensive test reports which are produced for every inspection activity carried out by our engineers.
Non-Destructive Testing (NDT) and Integrity Inspection services including spray dryer testing, tank, silo and heat exchanger testing services
Specialists in providing innovative testing and inspection methods.
The leading supplier of non-destructive crack testing and integrity inspection solutions for process equipment and equipment in the food, dairy, drink, chemical and pharmaceutical industries.
Independent Integrity Inspection Limited (INDEi) offers a wide range of innovative Non-Destructive Testing (NDT) and integrity testing methods for food, beverage and dairy processing equipment to help identify, prevent and eliminate microbial hazards in everyday consumer products.
Our non-destructive testing and integrity inspection methods have been proven over the past 20 years with highly qualified, trained and experienced technicians bringing together a combination of key skills and equipment to create unique partnerships with our clients to ensure the validation of their processing equipment and trust in their products.
The innovative crack testing methods are uniquely applicable for the various types of heat exchangers and pasteurisers, vertical and horizontal tanks and silos, pipes and process lines, spray dryer chambers/cones, external fluid bed dryers and evaporators enabling the confidence and prolonging the lifetime of the equipment under examination.
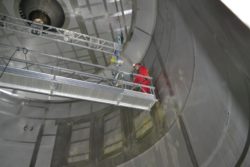
Innovative non-destructive testing and inspection services being carried out on a 9-metre diameter spray dryer using our unique access platform/gantry/bridge.
Our inspection/integrity testing services include:
- Pasteuriser and heat exchanger testing (plate, scraped surface, duo-plate, brazed and tubular);
- Heat exchanger servicing;
- Holding time (residence) testing;
- Tank, vessel, VAT and silo inspection;
- Spray dryer testing (chamber and cone inspection);
- Cyclone inspection;
- Vibro Fluid bed inspection;
- Bag filter housing testing and inspection;
- Bio-film validation, inspection and verification;
- Bio Finder quick microbial identification;
- Bio Scan;
- CIP effectiveness survey (Riboflavin testing);
- Evaporator tube inspection;
- Video endoscope examination and survey;
- Pipe inspection;
- Crack and leak detection/investigation;
- Flow rate confirmation and monitoring.
Food manufacturing, dairy and beverage production.
The food manufacturing, dairy and beverage production industry is a complex, global collective of diverse businesses that supply most of the food consumed by the world population.
The food and drink manufacturing industry amount to over 30 different industries. These include slaughterhouses, meat, poultry and fish processing, grain mills, maltings, bakeries, sugar confectionery, fruit and vegetable processing, oils and fats, margarine and edible oils, pasta, infant powder, baby foods and dairies. Drinks manufacture includes the production of soft drinks, beer and cider production, wines, spirits and whisky distilling. They directly touch the lives of every consumer from the moment they are born to the final day of their existence.
The introduction of laws, directives and standards such as ISO 22000, IFS (The IFS Food Standard is a GFSI (Global Food Safety Initiative) recognised standard for auditing food manufacturers. The focus is on food safety and the quality of processes and products) or BRC (The British Retail Consortium) is the leading trade association for UK retailing. Although the BRC food safety standard began in the UK, it is now recognised as a global standard. There are over 17,000 BRC certified sites worldwide, and a large network of BRC certification bodies in 90 countries) require all companies manufacturing food and beverages products to make their manufacturing processes transparent and as safe as possible. The possibilities for leaking and contamination from plate, tubular and SSHE heat exchangers, pasteurisers, process tanks, vessels and silos are endless.
A regular preventative maintenance programme (Preventive Plant Maintenance – PPM) instigated by the producer of the products will enable the risk to the consumer to be reduced and with regular crack testing and integrity inspection of the “Critical Control Points” will ensure compliance to the regulations and safety in the knowledge that product brand name and consumer safety will be continued to be regarded in a high position within modern-day society.
Full documentation for your quality management.
Experts at Your Service.
Leading food and beverage manufacturers rely on qualified and well equipped INDEI technicians to provide a professional service. We as a Company ensure process plant inspection and testing requirements are achieved efficiently and cost-effectively.
We combine our knowledge of food and beverage regulations and applications with the innovative range of testing equipment and experienced professionals to provide high-value products and tailored inspection solutions that meet your needs.
We support the manufacturer in determining the best solution for cost-efficiently maintaining production, quality and regulatory requirements.
We are the one source for all of the inspection methods needed to meet your specific requirements for accurate and reliable results, hygienic, trace-ability and maintenance management, specialists in heat exchanger testing, pasteuriser inspection, tank, vat, vessel, silo inspection and spray dryer testing.